Fiber optic cable construction is roughly divided into the following steps: preparation → routing project → fiber optic cable laying → fiber optic cable splicing → project acceptance.
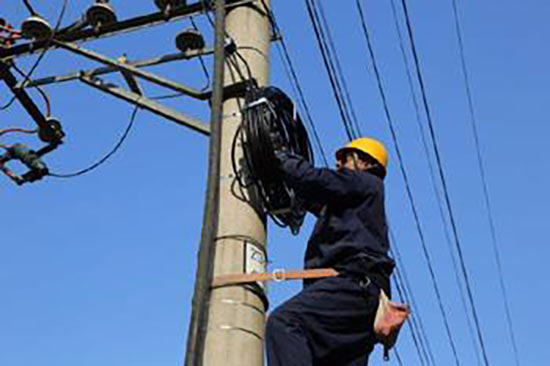
1. Preparation
(1) check the design information, raw materials, construction tools, and equipment is complete.
(2) set up a high-quality construction team. This is crucial because fiber optic construction than cable construction requirements are much more stringent. Any negligence in construction will likely cause increased fiber loss or even a broken core.
2. Routing engineering
(1) before laying the fiber optic cable should first do a serious survey of the route through the fiber optic cable. Understand the local road construction and planning, try to avoid ponds, wheat farms, gas stations, and other such potential hidden dangers. After the route is determined, the actual measurement of its length is done, accurate to within 50m. Also, add the natural bending and various reserved lengths during deployment. Various reservations also include insertion of bending in the hole, reservation on the pole, reservation at both ends of the joint, and other special reservations such as increased curvature of the horizontal plane. In order to make the fiber optic cable in the event of a break and then splice, should be left at every hundred meters with a certain margin, the margin length is generally 5% to 10%. Order according to the actual length needed and specify when winding the tray.
(2) Draw path construction drawings. Numbering on the pre-planted poles, draw the path construction diagram and state the number of each pole or underground pipe outlet pole and the length of the pipe. Set out the length and location of the need to leave a margin. This can effectively use the length of the fiber optic cable, a reasonable configuration so that the fusion splice point is minimized.
(3) Two fiber optic joints are best placed in a flat, geologically stable location. Avoid ponds, rivers, ditches, and roads, preferably located at the exit of the pole or pipe. Overhead fiber optic cable joints should fall next to the pole 0.5 ~ 1m or so, this work is known as the “distribution plate”. A reasonable distribution plate can reduce the fusion point. In addition, the construction drawings should also indicate the location of the fusion point, when the fiber optic cable breakpoint, it is easy to quickly use the instrument to find the breakpoint for maintenance.
3 fiber optic cable laying
(1) the same batch of optical fiber, its mode field diameter is basically the same, the fiber at a point of disconnection, between the two ends of the mode field, can be considered the same. Therefore, fusion splicing in this disconnect point can make the mode field diameter of the fiber fusion loss to a minimum. So require the cable manufacturer with the same batch of bare fiber, according to the requirements of the cable length continuous production, in each tray on the sequence of numbers, and are marked A (red), B (green) end, no jump number. Erection of fiber optic cables needs to be placed along the determined routing sequence according to the number and to ensure that the B end of the previous tray of fiber optic cable is connected with the A end of the next tray of fiber optic cable. To ensure that the splicing of the two fiber end field diameters is basically the same so that the fusion loss value achieves the minimum.
(2) overhead fiber optic cable can be used 72.2mm galvanized steel stranded wire for hanging cable suspension. Hanging wire and fiber optic cable to be well-grounded, to have lightning, electrical measures, and earthquake, wind mechanical properties. Overhead hanging wire and power line horizontal and vertical distance to more than 2m, from the ground to a minimum height of 5m, from the roof to a minimum distance of 1.5m. Overhead fiber optic cable hanging type there are three kinds: hanging wire hanging bracket hanging type, hanging wire winding type, and self-supporting type. Self-supporting type without steel stranded hanging wire, cable sagging, poor wind load, so commonly used hanging type.
(3) overhead fiber optic cable placement. Due to the length of the reel than the cable, the length may reach several kilometers, it is limited by the allowable rated tension and bending radius, special attention in the construction can not be pulled and the occurrence of kink phenomenon. General fiber optic cable can be allowed to pull about 150 ~ 200kg. The cable bending radius should be greater than or equal to 10 ~ 15 times the outside diameter of the cable, and the construction of the bending radius should be greater than or equal to 20 times the deployment. In order to avoid the fiber optic cable placed in the middle of the road, about 20m away from the pole, erected in two opposite directions, the first half volume, in the second half volume of fiber optic cable from the plate down. According to the “8” type way on the ground, and then deployment.
(4) in the cable placement, forbid the cable to play small circles and fold, twist, and to be equipped with a certain number of the intercoms. The “front walk followed by the cable on the shoulder” method of cable placement, can effectively prevent the occurrence of the back buckle. Also, pay attention to the even force, the traction force does not exceed 80% of the cable allowed, and the maximum instantaneous traction force does not exceed 100%. In addition, when erecting, in the bend of the cable or more complex terrain should be responsible for the vehicle is strictly prohibited to crush. Overhead deployment of fiber optic cable using pulley car, pre-hanging pulleys on the frame rod and hanging line (generally every 10 ~ 20m hanging a pulley), in the fiber optic cable leading up to the pulley, leading down to the pulley to reduce the drape, reduce the tension. Then wear a good traction rope between the pulleys, traction rope tied to the traction head of the cable, with certain traction to let the cable climb up the rack pole, hanging on the hanging line. Fiber optic cable hook spacing of 40cm, hook in the direction of the hitch on the hanger line to be consistent. Each pole should have a convex drip gutter, and each tray of fiber optic cable should be left at the joint with a pole length plus 3m of margin. So that the splice box ground fusion operation, and every few hundred meters to have a certain plate stay.
4. Fiber optic cable splicing
Common fiber optic cables are laminated, skeleton, and center bundle tube fiber optic cables. The color of the core is divided into this order, orange, green, brown, gray, white, black, red, yellow, purple, pink, and lime green, which is called the full-color spectrum of the core. Some fiber optic cable manufacturers use “blue” to replace a color in the color spectrum. Multicore fiber optic cable to different colors of fiber in the same bundle of tubes to become a group, so a multicore fiber optic cable may have several bundles. The cross-section of the fiber optic cable, the red bundle tube as the first bundle of fiber optic cable, clockwise for the white one, white two, white three …… last is the green bundle tube. In fiber optic splicing, the principle should be followed: the number of cores is equal. In the same bundle of the corresponding color fiber butt, the number of cores is different at the same time, in order to first connect the core of the larger, then the core of the smaller.
The above is “how to set up fiber optic cable?” I hope it can help you.